Meaningful work, such as in the oil and gas industry, is sometimes dangerous. The ever-present explosion and fire risk is chief among the many daily hazards that oil and gas workers face. It's a risk that can cause severe injuries, mess up operations, and cause significant damage to facilities and equipment.
Refinery fire and explosion
Industries take great care in preventing fires and explosions because they expose workers to fatal working conditions.
OSHA indicates that it is now considered standard practice to require flame-resistant clothing in the chemical and refinery industries. Stepping foot onto an oil and gas operation site, such as a refinery, without proper flame-resistant PPE is virtually unheard of today.
Several stats worth noting:
- Fires and explosions are the 3rd most fatal work injuries within the oil and gas industry.
- 16% of all oil and gas fatalities result from exposure to fires and explosions, which cause devastating burns.
- Since 2003, there have been more than 1,500 fatal occupational injuries in the oil and gas extraction industries.
- In 2017 alone, 23 fatal occupational injuries were due to fire or explosions in construction or support activities for oil and gas extraction.
With the above statistics clearly showing fire as a concern for oil and gas workers, wearing proper personal protective equipment (PPE) should not be taken lightly. While it is impossible to eliminate the risk of fire, the proper use of FR Clothing can minimize injuries and save lives.

MCR Safety SBS1027 Triple-Vented FR shirt worn in a refinery
Below, we provide deep insight into everything you need to know about the flame-resistant PPE options offered by MCR Safety. We provide the opportunity to educate consumers about the differences in protection options, including distinguishing between products using “limited flammability technology” vs. proper “flame resistance fabric”. You can never overprepare when better understanding the protective products available, especially proper FR Clothing.
Oil Refinery Explosion

October 23rd, 2019, will mark the 30th anniversary of the plant disaster in Pasadena, Texas, where 23 people died after a series of explosions caused by an ethylene leak. Inadequate safety procedures and refinery maintenance cuts contributed to the explosions.
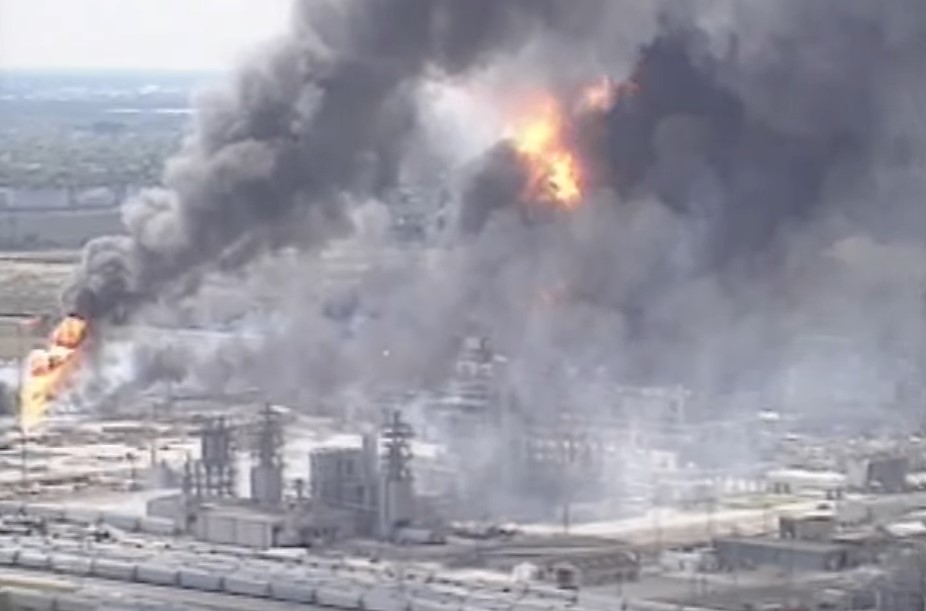
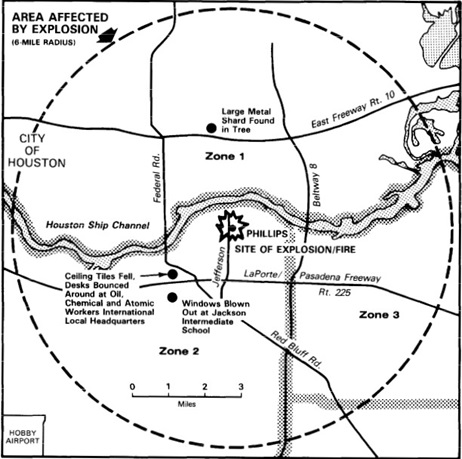
Click on the images above for ABC13 Houston’s video coverage of the explosions.
In a report revised in March of 2011,
FEMA outlined lessons learned from the tragic Pasadena explosions. Concerning worker safety, the Pasadena incident marked a significant change in the PPE requirements across the oil and gas industry. During a recent refinery visit, a worker told us that before the Pasadena explosions, workers wore whatever clothing they liked, and very little was safety rated. After witnessing workers’ clothing engulfed in flames and melting onto their bodies, the industry recognized that changes were needed to keep workers safe and minimize the risk of fires or explosions.
When a major accident like the Pasadena explosion occurs, the aftermath typically produces positive outcomes. In the case of PPE, workers now wear higher-quality flame-resistant garments and PPE. As a result of this horrible incident, there are now industry-wide flame-resistant clothing programs in place.
Flame Resistant Material
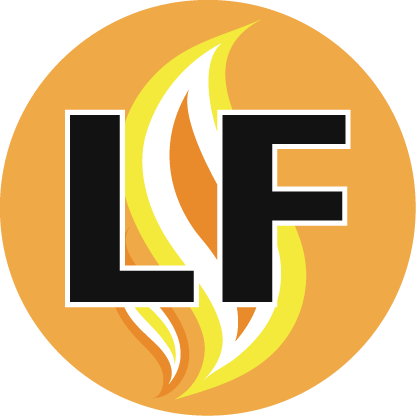
What is considered flame resistant material? It's an important question all should ask before they tackle a task that requires
FR Clothing. Flame-resistant apparel is vital for oil and gas workers because it mitigates burn injuries and provides insulation against second-degree burns. Yet safety managers and workers often overlook a crucial component:
the material used. Generally speaking, flame-resistant clothing is either made from a fabric whose fibers are inherently flame retardant or by chemically treating fibers to reduce flammability.
Not all protection is the same, though.
“Limited-flammability” garments are, strictly speaking, not fire-resistant; they may melt or burn when they come in contact with an open flame. Items deemed “limited flammability” have been chemically treated and tested to method
ASTM D-6413 to observe the materials’ reaction to an open flame.
Video showing ASTM D-6413 Open Flame test
ASTM D-6413 is not a standard. Let us repeat one more time:
ASTM D-6413 is not a standard. It's only a test method that determines a textile’s response to a common ignition source. MCR Safety highlights LF to show how the garment will self-extinguish within a matter of seconds once the source of the flame is removed.
This type of clothing is best suited for workers who may have incidental contact with heat, heated objects, or flames, working in a capacity where short-term protection is needed. Originally, limited-flammability gear was developed for welders in a protective vest, as welders required material that would not immediately catch fire from the flying sparks generated while welding.
Limited-Flammability apparel was initially developed for welders and cutters.
By self-extinguishing, LF materials help reduce the potential of burn injuries compared to straight PVC and polyester products not chemically treated with any flame-resistant properties.
Due to the oil and gas industry’s demand for this product, MCR Safety’s limited-flammability product line has expanded since the original CL2MLPFR vest became available for welders. We now offer multiple
high-visibility vests,
rain gear, coats, and reflective polyurethane/cotton suits; all produced using chemically treated materials and offering limited flammability. The 5182 and 5182S garments have been an oil and gas industry favorite for over a decade. Below are some of our most popular LF styles.

The 5182's stretch PU material provides ultimate mobility and comfort.

What's the primary reason users love wearing our rider coats? The extended PVC/polyester in this rain gear keeps workers dry without wearing a full rain suit. We protect users by offering three styles: a standard, a flame-resistant, and a silver reflective design.
Limited-flammability products are considered a cost-effective flame apparel solution. With that said, a company needs to carefully evaluate the hazards employees encounter before choosing this type of protection. As outlined above, explosions, fires, and burns are serious injury hazards faced by workers in the oil and gas industry.
Remember, LF garments are not for protection against flash fires. You will need to wear safety clothing tested to flash fire hazards.
What is a flash fire hazard?

Plant explosions, like the Pasadena disaster, are not the fire incidents that affect workers daily. Flash fires are much more common and are the hazard that concerns oil and gas workers most due to the severe thermal injuries a worker’s body may sustain.
A flash fire is a sudden, intense, rapidly moving flame in an environment where fuel, vapors, dust, and air combust. The vapors or particles that ignite and explode seriously threaten workers, causing extensive harm to equipment and people. As
OSHA points out, the intensity of a flash fire ultimately depends on the size of the gas or vapor cloud that ignites.
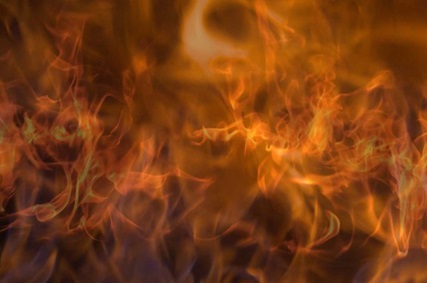
Because a flash fire quickly consumes fuel, it lasts only 3 seconds or less. In that short time, though, temperatures may reach 1000-1900°F.
The potential likelihood of a flash fire rises during
upstream drilling activities once drilling hits formations of hydrocarbons and gas. However, keep in mind that flash fires are always present across
midstream and
downstream oil and gas operations. Bringing well fluids to the surface by separation and storage poses a flash fire hazard for workers. Here are some general areas where flash fires and general fires are a definite concern:
- Heat source that sparks fire
- Cylinder and fuel storage areas
- Equipment openings, such as valve changes
- Gauging
- Hot surfaces
- Hot work, such as welding or using spark-producing tools
- Inreased static electricity
- Maintenance operations
- Motor generator areas
- Operating a degasser
- Operating electrical tools
- Tank heating
- Using open flames
- Well servicing – cementing, fracturing, plugging abandoned wells, wireline operations, etc.
- Working with open flames
- Working around electrical systems
Combating flash firest requires actual flame-resistant FR clothing. Non-FR clothing, such as PVC rain suits and even “limited-flammability” apparel, can ignite and provide an additional fuel source, dramatically increasing burn injuries.
Flame Testing of Fire-Resistant Results

Actual “flame-resistant” garments resist burning and withstand heat, thereby providing greater protection than limited-flammability garments. True flame-resistant garments offer the best protection against flash fires for oil and gas workers because they will not ignite and continue to burn after a flash fire has ended. “Limited-flammability” garments will ignite and should therefore be avoided if flash fires are a concern.
Flame-resistant garments are engineered with either inherently flame-resistant fibers with flame resistance built into the material’s chemical structure or chemically treated with higher-quality flame-resistant materials. MCR Safety’s inherent FR materials include Nomex® material and modacrylic/aramid blended fabrics. Acrylic fibers are poor conductors of heat and are difficult to ignite.
The
National Fire Protection Association (NFPA) is a leading resource on fire, electrical, and other related hazards. They set codes and regulations that define flame resistance standards. The
NFPA 2112 Standard sets 17 tests for garments to meet the flame-resistant protection standards for flash fire. These include tests for the following:
- ASTM F1930 manikin testing
- Colorfastness
- Flame-resistance
- Heat-resistance
- Label legibility
- Shrinkage
- Tensile strength
- Tear strength
- Thread melting
The most recognized test is
ASTM F1930, the Manikin Test, which conducts a fire simulation at 3 seconds with a pass/fails rate of 50% total body burn.
Burn Injury

Burn injuries are described in terms of the percentage of the body’s surface area that is burned. When a body burn percentage is below 25%, there is a 90% chance of survival. If the body burn percentage reaches 50%, the odds of survival drop considerably but are still optimistic. A burn requirement of 50% of the test manikin or less is required for an FR garment to meet NFPA 2112.
The American Burn Association reports that the primary causes of burn injuries are fire-flame, scalds, contact with a hot object, and electrical and chemical burns. The graph below shows the chances of survival from a burn injury.

Once the body burn percentage exceeds 50%, survival rates drop precipitously, especially for older individuals. Workers in their 50s, with burns over half their body, have less than a 20% chance of surviving. The best way to survive a job-site fire is to protect as much of the body as possible.
MCR Safety’s T
riple-vented FR shirts combined with FR jeans provide wearers with maximum protection and are rated to minimize body burns to as little as 8%.
.png?h=397.333&w=746&hash=F6AC1036F4505217DF7CBB62C9473348)
A worker wearing a triple-vented MCR Safety coverall stands an excellent chance of surviving flash fires and burn injuries.
MCR Safety FR Clothing

MCR Safety is recognized for having one of the widest PPE selections for the oil and gas industry. As you can imagine, we have many FR Clothing options to choose from and continuously add new styles. Below are some of the newest additions to MCR Safety’s FR product line. Click on any image below to learn more.

Flame Resistant Clothing Outerwear Vest

At only 5.5 ounces, our Summit Breeze®️ FR Work Shirt is one of the industry’s lightest weight FR rip-stop shirts.

Spending all at a refinery can be tough on you and your safety gear. MCR Safety's lightweight F.R. coveralls weigh only 5.5 ounces and are triple-vented, so you'll stay cool and comfortable for the entire work shift.
.png?h=441.667&w=833.333&hash=1C06052B843E4191B8D0D7E755275A02)
Our lineup of FR hi-vis garments, which includes rainwear, coveralls, and safety vests, are designed to keep you visibly protected and dry. Big Jake 2 FR rainwear is tested to the stringent ASTM F2733 standard specification for flame-resistant rainwear.
.png?h=458&w=795&hash=0A3FC908D7CC7988612314F2800D8D24)
The LST 6.5 oz is the lightweight shirt features a raglan sleeve design, which fits comfortably and allows for ease of movement.

The PD2 jeans, made with 98% cotton and 2% spandex, are stretchy and offer more flexibility at work!

Remember, we also manufacture flame-resistant gloves, like the MU3624GFR with a Nomex® back.
For a look at all of MCR Safety’s FR Clothing, click here. Other helpful resources:
Common Questions

What is a flame-resistant material used in PPE?
- Numerous FR materials are available, ranging from Nomex®, Westex®, and MCR Safety's Summit Breeze ripstop material. You can sort by material on our FR online catalog.
Is Kevlar material flame resistant?
- Kevlar® fiber is inherently flame-resistant and will not burn, support combustion, or melt, making it a smart choice for those who encounter both cut and heat on the job. However, while it is flame-resistant, it is not flame-proof and can still burn when under sustained exposure to fire. It's also important to recognize and evaluate the fiber thickness and combined material. Many of MCR Safety's Kevlar products are blended with other materials that may not be flame-resistant.
Which zone of burn injury sustains the most damage?
- The "zone of coagulation" is a term used in burn medicine to describe the primary area of a burn injury where the tissue sustains irreversible damage and the tissue is necrotic or dead.
Which type of burn injury requires skin grafting?
- Full-thickness or third-degree burns are the most severe types of burn injuries. They damage all first layers of the dermis and the second layers of the epidermis' underlying tissues and nerves, causing permanent loss of function and disfigurement.
Why are burns so painful compared to other injuries?
- All burns are excruciating due to the nature of the injury, as they cause damage to the nerves that transmit pain signals to the brain.
What can cause oil rig explosions?
- Rig explosions occur due to several reasons. Some examples include malfunctioning equipment, such as valves, that begin leaking and eventually lead to ignition. Improper maintenance is another example, as human error can easily lead to an explosion. Anywhere an ignition source occurs, such as open flames, electrical sparks, and hot surfaces, there is potential for an explosion. All of these reasons are why following safety procedures is a must.
What year was the bp oil rig explosion?
- The BP oil rig explosion occurred on April 20, 2010.
What is the flash fire hazard flash point?
- The flash point is a liquid's minimum temperature at which it can give off an ignitable mixture in the presence of an ignition source. For example, substances with low flash points, such as gasoline and propane, are highly flammable and quickly ignited. In contrast, liquids with high flash points, such as water, are not flammable.
FR Clothing for Oil and Gas

MCR Safety dedicates its efforts to producing the personal protection equipment workers require in hazardous working conditions. Workers go into harm’s way daily and risk their lives against potential flash fires. Don’t they deserve the best protection available? Let us help you help them find the proper flame-resistant protection.
Do you have questions about MCR Safety’s oil industry PPE?
Contact us! We’re happy to answer your questions, and we’ll be happy to help you find the perfect PPE gear for your company’s needs. For insight into all oil and gas sectors, check out our
Oil and Gas Industry pages. Just click on the image to learn more.
Click the image below to leave us comments, questions, or concerns.
REQUEST A DISTRIBUTOR QUOTE
TRY IT OUT
For over 45 years, MCR Safety has proven to be a world leader in gloves, glasses, and garments. Whether it's working in refinery, assembling products with polyester PU gloves, or working at a construction site, we are there, providing solutions to workplace hazards. It's all part of our commitment to protect people.
No matter your industry, we have the personal protective equipment you need.

Click the above image to be taken directly to our PPE online catalog.

Learn more about MCR Safety by checking out our most recent video. For more information, browse our website, request a catalog, find a distributor, or give us a call at 800-955-6887.